Introduction Controlling Management and Process of Controlling
Controlling management is a part of the managerial process. Control is one of the most important elements of management. Control is a process which guides activity towards some predetermined goals. Planning and controlling are twins of management functions. It means measuring the actual performance and taking corrective action.
Definition – Controlling Management
“Control is checking the current performance against predetermined standards contained in the plans with a view to ensure an adequate progress and satisfactory performance”
“Controlling is the measurement and correction of performance in order to make sure that enterprise objectives and the plans devised to attain them are accomplished”.
Characteristics of Control – Controlling process is universal
Control is an essential function in any organization whether it is an industrial unit, university, government office, hospital
Control is a continuous process
Controlling is a never ending activity on the part of managers. It is a non-stop process. The manager watches the operation of the management and to see whether they are going towards the desired end and if not, actions are not taken to correct them.
Control is action based
Action is an essential element of the control. It is the action which ensures the performance according to the decided standards.
Control is forward looking
Control is linked with future not past. A proper control system prevents losses and minimizes wastages. It acts as a preventive measure.
Control is closely related to planning
A plan gives the direction to various business activities while control verifies and measures the performance of these activities and suggests proper measures to remove the deviations.
Need of Control
- To minimize dishonest behaviour of employees
- To discover deviations in the management
- Control can minimize the mistakes
- To indicate corrective action
Importance of Controlling
Policy verification
A control helps to this review, revise and update the plans. In process, organization and management can verify the quality of various policies.
Adjustments in operations
A control system acts as an adjustment in organizational operations. Control provides this clue by finding out whether plans are being observed and suitable progress towards the objective is being made to correct any deviations, if necessary.
Psychological pressure
A control process puts d psychological pressure on the individual for better performance. The sound control system inspires employees to work hard and gives the better performance.
Coordination
A control helps to emerge the coordination of the subordinates in the organization. Control ensures the coordination of activities of different departments through unity of direction.
Employee morale
A control creates an atmosphere of order and discipline in the organization. Control contributes order and discipline in the organization.
Efficiency and Effectiveness
Proper control ensures the organizational efficiency and effectiveness. The organization is effective, if it is able to achieve its objective. Since control focuses on the achievement or organizational objectives, it necessarily leads to organizational effectiveness.
Limitations of Controlling
- Controlling management is expensive and time-consuming process.
- Control cannot consider the external factors, such as technological changes, political factors, social changes, government procedures etc.
- Human behaviour and employee morale also cannot be measured.
Process of control – Establishing standards
- This is the first step of the control process.
- Standards may be expressed in quantitative or qualitative terms.
- A standard is a criterion against which results can be measured.
- Generally, standards shall be accurate, precise, acceptable and workable.
- Volume of products, man hour, costs, revenue, investment etc. They are quantitative standards.
- Good will, employee morale, motivation etc. These areas are qualitative standard.
Measuring performance – Controlling Management
- Measurement of actual performance does not mean has knowing what has happened but also what is likely to happen.
- The performance should be in quantitative terms.
- The measurement technique may be personal observation, sample checking, performance report etc.
Comparing actual with standards
- To find out the deviations and identify the causes of such deviations.
- The employee morale and effectiveness of human resources statements, charts help to compare the performance quantitatively against the already got standards which got.
- This approach will give the correct, quick and favourable results.
Finding out deviations – Management
An efficient manager easily finds out to locate the deviation points properly.
To find out the cause of deviations, the manager will have to depend on a proper accurate and timely information.
If the deviation between standard and actual performance is beyond the prescribed limit, an analysis of deviations is made to identify the causes of deviation.
Correction of deviations
Corrective action is essentially with correcting deviations from planned performance.
Deviations may be in accurate forecast poor communication, defective machines, lack of motivation etc.
For the correction of deviations, management should take necessary action and implement them so that in future these deviations and mistakes are minimized.
If corrective action is not taken properly on time, it will lead to heavy losses.
Critical Control Points and Standards
The points selected for control process is called critical points. The principle of critical point control is one of the most important control principles. The effective control requires an attention to those factors critical to evaluate the performance against plans.
- Physical standards
- Cost standards
- Capital standards
- Controlling Management
- Revenue standards
- Program standards
- Intangible standards
- Goals as standards
- Strategic control
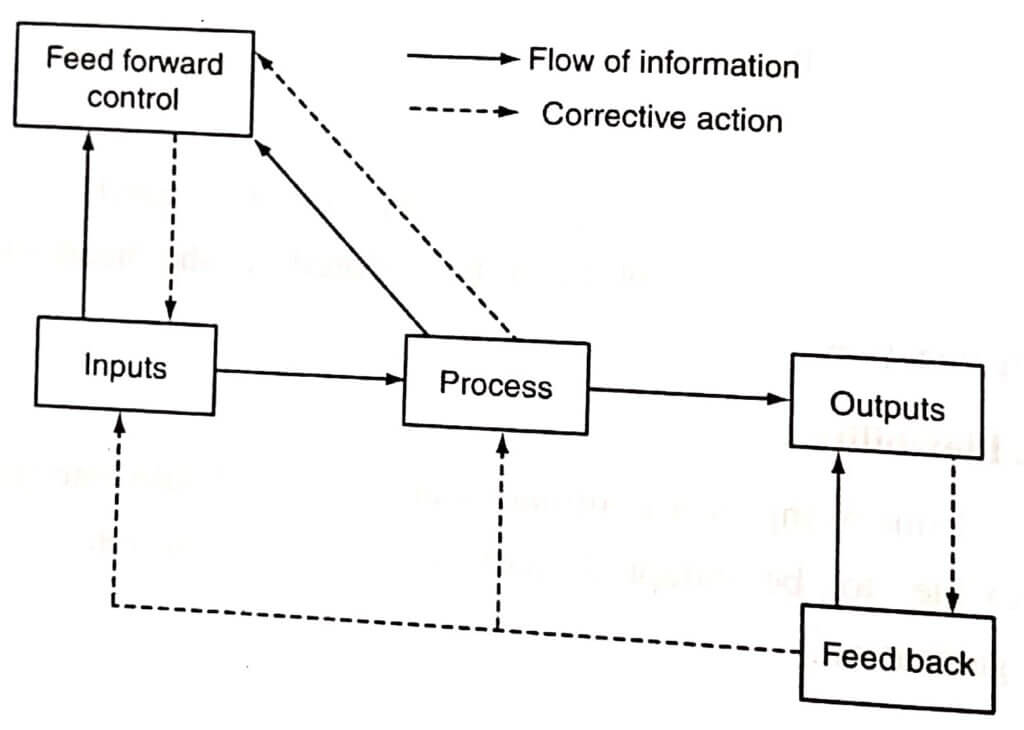
Physical controlling management standards
These standards are in quantitative terms, such as number of units per man-hour or in qualitative terms, such as fastness of colour or durability of goods produced. Physical standards may also reflect the quality, such as hardness of bearings, durability of a fabric.
Cost standards
These are the monetary cost directly or indirectly involved in production. Example: Labour cost per unit or per hour, material cost per unit, machine-labour costs.
Capital standards – Controlling Management
These are arising from the application of monetary measurements to physical items. Example: Ratios of current assets to current liabilities, fixed investment to total investment.
Revenue standards
These are the monetary value of sales. Example: Sales for capital in a given market area.
Program standards
A manager installs a variable budget program for improving the quality of sales force.
Intangible standards
These standards are difficult to set either physical or monetary measurements. Example: District sales office, accounting benefits of training department. For example, what standard can a manager use for determining the competence of the divisional purchasing agent?
Goal as standards
These are qualitative or quantitative goals at every level of management.
Strategic control
Strategic control facilitates comparisons of intended goals with actual performance. They also provide the opportunities for learning, which in tar is the basis for organization change.
Interrelationship between Planning and Controlling
Planning is the foremost function of the management which decides in advance what is to be done and who will do it and how where and why? Control means comparing the operating results with the plans and taking corrective action where results deviate from the plans.
The management process begins with planning and ends with control. Control is necessary for every planned activity. Planning determines the standards for performance. Control helps in achieving them.
Planning is the first step and control is the last step in the process of management. The control points out the deviations of plans and suggests remedial actions which are needed to improve the future plans. Planning and control are the inseparable twins of the management.
Feed forward controlling management
This control involves the evaluation of inputs and taking corrective action before a particular operation is completed. It is preventive in nature. This control allows the corrective action to be taken in advance of the problem.
For example, cash budget in the organization is the type of control. The finance manager prepares the next year flow of cash budget in the organization. If there is a shortage of finance for a particular month, he is responsible to arrange for bank loans or other alternatives.
Feed forward in human system: There are many examples of feed forward control in human system. A hunter will always aim ahead of a duck’s flight to correct for the time lag between a shot and hoped for hit.
REQUIREMENTS FOR EFFECTIVE CONTROLLING
- Suitability – A sound control system must suit the needs of the enterprise. The control must be tailored to the need of an organization.
- Flexibility – Controlling is a continuous activity, it should enough be flexible to be adapted with changing conditions of an organization.
- Economical – The control system should be less expensive. Expensive control should be avoided.
- Simple bur – A good control system should be simple to understand to the administrator. Complex control system creates confusion in the organization.
Controlling Management by Exception
- Management by exception is an important principle of management.
- The deviation by comparing the actual performance compare with the standard performance which is not significant should be avoided.
- In this case follow up process is unnecessary.
- If deviations are important or more significant, the deviations can be reported to the management.
- Management concentrates only the critical problems which can be given higher benefits to the management.
- A manager who would interact every minor problem in the organization makes the management ineffective.
- This principle suggests that the top management should concentrate only major and significant problems.
- Minor problems hand over to their subordinates.