Optical Fiber Connectors
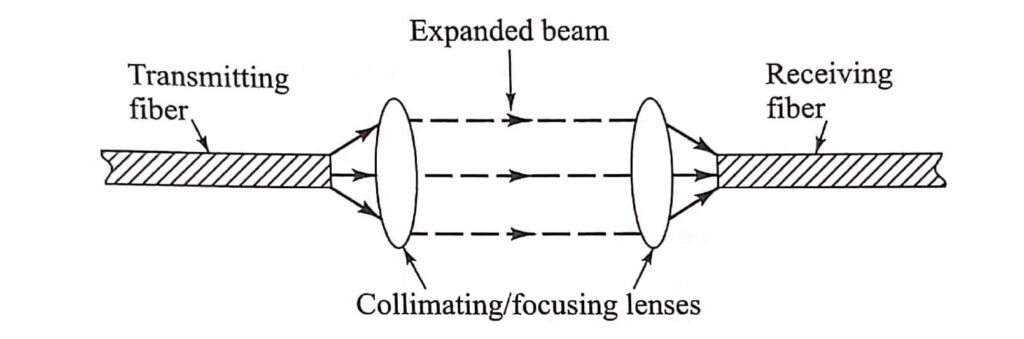
A wide variety of optical fiber connectors has evolved for range numerous different applications. Their uses from simple single channel fiber to fiber connectors in a benign location to multichannel connectors used in harsh military field environments. Some of the principal requirements of a good connector design are as follows:
- Low coupling losses. The connector assure assembly must maintain stringent alignment tolerances to low mating losses. These low losses must not change significantly during operation or after numerous connects and disconnects.
- Interchangeability. Connectors of the same type must be compatible from one manufacturer to another.
- Ease of assembly. A service technician should readily be able to install the connector in a field environment; that is, in a location other also be than the connector factory. The connector loss should fairly insensitive to the assembly skill of the technician.
- Low environmental sensitivity. Conditions such as temperature, dust, and moisture should have a small effect on connector-loss variations.
- Low-cost and reliable construction. The connector must have a precision suitable to the application, but its cost must not be a major factor in the fiber system.
- Ease of connection. Generally, one should be able to mate and demate the connector, simply, by hand.
Connector Types – Optical Fiber Connectors
Connectors are available in designs that screw on, twist on, or snap into place. The most commonly used connectors are the twist-on and snap-on design. These include both single channel and multichannel assemblies for cable-to-cable and for cable-to-circuit card connections. The basic coupling mechanisms used in these connectors belong to either the butt-joint or the expanded-beam classes.
Butt-joint connectors employ a metal, ceramic, or molded-plastic ferrule for each fiber and a precision sleeve into which the ferrule fit. The fiber is epoxied into a precision hole which has been drilled into the ferrule. The mechanical challenges of ferrule connectors include maintaining both the dimensions of the hole diameter and its position relative to the ferrule outer surface.
Image shows two popular butt-joint alignment designs used in both multimode and single-mode fiber systems. These are the straight-sleeve and the tapered-sleeve (or biconical) mechanisms. In the straight-sleeve connector, the length of the sleeve and guide ring on the ferrules determine the end separation of the fibers. The biconical connector uses a tapered sleeve to accept and guide tapered ferrules. Again, the sleeve length and the guide rings maintain a given fiber-end separation.
An expanded-beam connector, illustrated in image, employs lenses on the ends of the fibers. These lenses either collimate the light emerging from the transmitting fiber, or focus the expanded beam onto the core of the receiving fiber. The fiber-to-lens distance is equal to the focal length of the lens. The advantage of this scheme is that, since the beam is collimated, separation of the fiber ends may take place within the connector. Thus, the connector is less dependent on lateral alignments. In addition, optical processing elements, such as beam splitters and switches, can easily be inserted into the expanded beam between the optical fiber connectors ends.
Single-Mode Fiber Connectors
Because of the wide use of single-mode fiber optic links and because of the greater alignment precision required for these systems, this section addresses single mode connector coupling losses. Based on the gaussian beam model of single-mode fiber fields, the following equation gives the coupling loss (in decibels) between single mode fibers that have unequal mode-field diameters (which is an intrinsic factor) and lateral, longitudinal, and angular offsets plus reflections (which are all extrinsic factors).
Connector Return Loss
A connection point in an optical link can be categorized into four interface types.
These consist of either a perpendicular or an angled end-face on the fiber, and either a direct physical contact between the these methods has a basic application fibers or a contact employing an index-matching material. Each of for which it is best suited. The physical-contact type connectors without index-matching material are traditionally used in situations where frequent reconnections are required, such as within a building or on localized premises. Index-matching connectors are standardly employed in outside cable plants where the reconnections are infrequent, but need to have a low loss.
This section gives some details on index matched and direct physical contacts, and discusses angled interfaces. In each case, these connections require high return losses (low reflection levels) and low insertion loses (high optical-signal throughput levels). The low reflectance levels are desired since optical reflections provide a source of unwanted feedback into the laser cavity. This can affect the optical frequency response, the linewidth, and the internal noise of the laser, which results in degradation of system performance.
Image shows a model of an index-matched connection with perpendicular fiber end faces. In this figure and in the following analyses, offsets and angular misalignments are not taken into account.
The connection model shows that the fiber end faces have a thin surface layer of thickness h having t high refractive index n, relative to the core index, which is a result of fiber polishing. The optical fiber connectors core has an index no, and the gap width d between the end faces is filled with index-matching material having a refractive index n1. The return loss RL in decibels for the index-matched gap region is given by
RLIM= -10 log 2R11-cos4πn1dλ
where
R1=r12+r22+2r1r2 cos ϑ1+r12r22+2r1r2 cos ϑ
is the reflectivity at a single material coated end face, and
r1=n0-n2n0+n2 and r2=n2-n1n2+n1
faces are polished at an angle θ with respect to the plane perpendicular to the fiber axis. This angle is typically 8°. If I and It are incident and throughput optical power intensities, respectively, then the transmitted efficiency T through the connector is
T = It Ii = (1-R)2(1-R)2+ 4R sin2(β/2)
where
sinθ0sinθ=nn0, β = 4πn1d cosθλ, and R = n0-n1n0+n12
- See More : Optical Comparator
- See More : Point to point links
- See More : Radio over fiber links
- See More : Penalty power